Industries
The smart future of manufacturing companies
09/01/2019 | Written by: Katleen Aems
Categorized: Industries | Internet of Things (IoT)
Share this post:
Maximum productivity and minimal downtime, an optimal supply chain and the retention of operational know-how. That is what manufacturing companies and their leaders want. Moreover, it is precisely what so-called ‘cognitive manufacturing’ can provide. This was evident from a recent interactive webinar, where IBM specialists presented the smart future of the manufacturing industry.
Victor Sánchez Chumillas, an IBM business architect, advises customers in the Benelux on industry-specific cognitive applications. He shares that the benefits companies usually look for vary from improving performance on the production floor to lowering costs, or to engage with end-users and customers. Key elements are the internet of things. The collection and availability of data from various sources. And the intelligent processing of this data for analysis, decision making and insight.
Most of the time it is all about applying data in a smarter way. The cognitive aspect is not so much about ‘learning’, but about ‘understanding’. This counts for data coming from the manufacturing process. As well as for data coming from transactional systems or even from the outside world. The nature of all this data also varies considerably. From sensor to transaction data. From structured to unstructured items such as photos, voice, e-mails and messages on social media. All these different kinds of data sources and types require a platform powerful enough to bring it all together.
Value creation
When we ‘understand’ all this data, the creation of value is within reach according to Victor Sánchez. “For example, the interaction between man and machine can be improved through proper processing and analysis. Think of how you could better support operators. Or where to deploy chatbots. You will make better decisions thanks to advanced data analysis.”
Machine learning plays a role in discovering patterns that provide insight. For example, into the production process or the performance and maintenance requirements of machines. This can increase the efficiency of devices and processes, fully automated or otherwise. An intelligent handling of data ensures better performance. Better stability. Better quality products. And ultimately the creation of new services.
“The data collection is fundamental”, says Victor Sánchez. “This requires a well thought-out approach. Because by simply collecting all available data in a data lake leads to a data swamp. You will not be able to find anything anymore. The supporting technology must take into account the life cycle, the findability and usability of the data.”
Predictive analytics
Ashok Kumar is Global Industry Leader in Manufacturing for Watson IoT. During the webinar he talks about a unique use case. An IBM customer in the fast moving consumer goods successfully implemented artificial intelligence and cognitive manufacturing based on the Waston IoT platform. The value lies in predictive and diagnostic analytics, which greatly improved the operational process.
Several thousand data tags within two production lines constantly monitor progress, maintenance and quality. The structured and unstructured data generated in the process is transported via a gateway to the IBM Cloud. After processing, this leads to an optimal insight into the performance and functioning of the machines.
“Less disruptions and a more efficient process based on operational KPIs lead to large savings in money, time and people. The quality of the products has also increased. There is much more insight into the total supply chain”, says Kumar. The technology used is a collection of OT/IT connections, the Watson IoT solution, system integration, analytical services, the enterprise maintenance system, and the accelerators for predictive maintenance, production optimization and quality optimization. The specialist highly recommends companies to start organically, through a modular implementation.
Webinar poll
On the poll question ‘what is the most important area where AI could play a role in your organization’, 45 percent of the webinar attendees saw opportunities for maximizing plant productivity in combination with preventing downtime, where 33 percent called ‘innovating and optimizing the supply chain’, and 22 percent ‘ensuring retention of critical operational know-how’.
On the journey to Industry 4.0 45 percent of the webinar audience is ‘developing an Industry 4.0 technical framework’ and ‘exploring the role partners will need to play’. Of the attendees 22 percent would like to know how Industry 4.0 can be applied, where another 22 percent has already a basic understanding of what Industry 4.0 can do. A minority of 11 percent is beginning to build a case for Industry 4.0 to put in front of senior leadership.
Learning phase
Tobias Stöckel from IBM’s Watson IoT Center in Munich, creates prototypes around industrial IoT. He emphasizes that the implementation of new possibilities should ideally be preceded by a learning phase. Tobias refers to a case of a cement manufacturer capable to maximize productivity and prevent downtime, while at the same time assuring retention of operational know-how.
The company improved on three dimensions. First the availability of the machines. Then the performance and throughput efficiency of processes, energy and material consumption. And also the improvement of product quality. Machine learning is used to analyze and correlate different sources of data. “Information from the traditional production process is combined with sensor data. But also with, for example, weather forecasts and current and expected humidity. Actually everything that influences the process. IBM Watson hereby gives specific recommendations to the operators. Especially the energy consumption decreases considerably, while the process improves. Knowledge management is also better assured because intuitive expert knowledge is retained and remains available.”
Stöckel emphasizes that cognitive manufacturing is not about replacing human knowledge and expertise. It is but about optimally supporting experts: building a relationship of trust between people and machines.
Proof of value
Various industrial solutions are available so companies and their leaders can easily start the first experiments. This way they can scale up quickly if required. For example, in the context of intelligent assets and equipment, where the operation of machines is continuously monitored and analyzed. Cognitive technology can be used to improve operational processes. Resource optimization in turn relates to the manufacturing or supply chain.
“Anyone who wants to start should prefer the ‘proof of value’ to a proof of concept”, says Victor Sánchez Chumillas. The latter has after all been proven for a long time. “The point is to determine which technology is of value within the organization. Then you quickly start a pilot, where you can achieve results within a few weeks. A cognitive manufacturing process does not have to take months.”
If you want to know more about how you can transform your company to be Industry 4.0 ready, we kindly invite you to watch our on-demand webinar or visit our smart manufacturing website
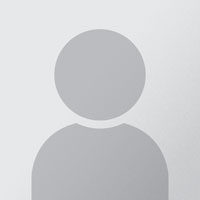
Brand Amplification Lead Benelux
The Digital Operational Resilience Act for Financial Services: Harmonised rules, broader scope of application
The Digital Operational Resilience Act – what and why As part of the European Commission’s Digital Finance Package, the new Digital Operational Resilience Act, or in short DORA, will come into force in the coming period. The aim of DORA is to establish uniform requirements across the EU that improve the cybersecurity and operational resilience […]
Banking on empathy
Suppose you’re owning a small boutique wine shop and have gone through two difficult years because of the Covid-19 pandemic. As the pandemic seems to be on its way back, it is time to revitalize the shop. And this causes direct a huge challenge: the wine stock needs to be replenished but you have used […]
Red Hat OpenShift en MAS – een gouden combinatie
De nieuwste versie van IBM Maximo Application Suite (MAS) draait sinds kort op een Red Hat OpenShift-infrastructuur. Welke nieuwe mogelijkheden brengt dat met zich mee en wat zijn daarvan de voordelen? In dit blog gaat Marc Loos, Evangelist Hybrid Cloud, Enterprise Container en IBM Cloud Advocate hier dieper op in. Red Hat OpenShift is een […]